今 年4月,大方公司对该生产线进行规划筹建,按照单件流、准时化的思想进行设计,通过调整工序布局、改进工装工艺、物流配送及作业习惯等方式,重点改善产品 质量、生产效率、场地利用等方面。经过对设备改造、整合优化工序,各工序间的节拍平衡率由原来的51.7%提高到81.3%。滚杠传送加快了产品的流转速 度,不仅降低了劳动强度,还大大减少了等待浪费,提高了工作效率,减少了安全隐患。单件流的生产思想已得到员工认可,生产周期由原来的5.5天缩短至 2.8天,制造计划完成率提高到96.6%,同时在制品存量大幅降低。双枪龙门焊和利用余料制作的翻转工装,有效保证了产品质量,一等品率由年初不足4% 提高到17.3%,线上所有产品实现了无售后的好成绩。该线还改变了工人的作业方式,由行业普遍的蹲地、弯腰作业转变为站立工作,降低了劳动强度,减少了 职业病的发生,并且人均收入提高20%以上。通过定置管理,节约场地300余平方米。经过几个月的运作,精益管理的成果已初见成效,员工的思想意识得到转 变,各班组由抵触、拖延到主动要求参与到精益生产中,为公司后期推广精益管理奠定了良好的基础。
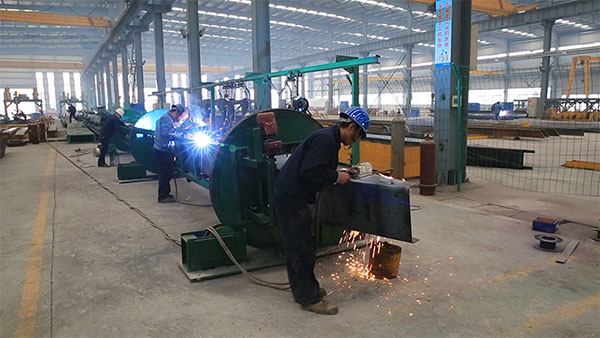
公司还将继续挖掘潜力,不断改进,优先保证,发挥该线的最大效益。通过加强跟踪,广泛宣传和培训,固化成果,做到“质量、效率、效益”三个提高,让精益管理思想在起重行业开花结果!