0/100
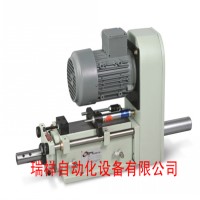
台湾钻孔动力头FD56-100
来自:东莞瑞先祥自动化设备有限公司
12000人民币
发布时间:2012-11-28
关注次数:483
产品参数

商品详情
方技动力头(主轴头) 钻孔攻牙主轴头属动力部件,可钻孔、攻牙作业,也可配装多轴器,提升效率。是精度要求较高之产品加工,量产型产品可配作自动化作业,例如:摩托车零部件、汽车零部件等要求高及量产化的部件。可设计成钻孔攻牙切削加工专用机。 台湾方技主轴头(动力头): 1、采精密研磨螺纹样规,适合精密高之攻牙工。 2、外装式螺纹样规,更换容易、快速。 3、可装置立卧式两用。 4、可装配多轴器用。 台湾方技主轴头特点(动力头): 1.由于刀具进给与旋转是同步进行,因此很薄或很软的材料也能被有效地加工, 2. 适应性强,可以很方便地调整加工螺纹的直径,螺距及行程 3. 行程长,附件种类多,可以方便地将单轴攻丝头换成多轴攻丝头,能同时满足用户小批量和大批量生产需要 4. 方技公司,不断响应用户对钻孔加工的高速化,高精度化要求的方技钻削动力头,为您准备了最适合于贵公司需求的钻削动力头 5. 钻削动力头,风电式底座型 6. 主轴旋转由电力,进给及控制由压缩空气压力进行的性能价格比最卓越的钻削装置,根据加工条件可以从丰富的机种中选择最适合的型号 7. 底座型结构的高精度,高刚性钻削装置,主轴电动机采用了高性能,高功率的电动机,具有从低转速到高转速广泛的类型。 全气控气动卧式三面双工位钻孔、铣槽组合机床的设计
1 问题的提出及设计方案的确定 我公司燃气灶中气阀芯(见图1)从单轴纵切自动车床加工后,仍有2个孔、3条槽需要加工。以前加工的工艺方法是用仪表车床开槽,用台钻钻孔,分5道工序完成。这种加工方法存在以下缺点:①因多次定位,零件加工精度难以保障;②生产效率低,完成这5道工序需5台机床,5个工人,生产节拍为40 s;③自动化程度低。为了解决这些问题,我们设想把这5道工序合为1道工序,安排在同一机床上1次装夹完成加工。根据被加工件为铜材,材质较软,切削力小的特点,设计了1台采用全气控气动加工卧式三面双工位钻钻孔、铣槽平面组合机床。
2 机床的主要结构 1) 机床结构形式
该机床有钻孔动力头装置、铣削动力头装置、专用夹具、滑台、床身等。整个机床加工采用两工位布置,考虑到被加工件切削量小,本机床不设冷却系统(见图2)。
2) 特点
a) 钻孔动力头:采用日本SUGINO公司生产的气动进给动力头。其主要技术参数为最大钻孔直径8 mm,最大行程100 mm,主轴径向跳动精度≤0.01 mm,滑套轴线与固定套轴线移动方向平行度≤0.02 mm。其特点是加工精度高,动力头完全是气控、气动,配以可调节流器和液压阻尼器,可以实现对快进和工进速度的任意调节,且安装方便。
b) 铣削动力头装置:铣削头为自行设计,考虑它作为以后的通用件,设计此动力头在X、Y、Z3个方向均可以在一定范围调整。该铣削头装在滑台上,通过气缸驱动加上液压阻尼器,可进行快进和工进,在铣头原位和终点设置了气动行程开关。
c) 滑台:该滑台采用燕尾导轨,内有可调镶条,刚性好,工作稳定可靠,由气缸驱动。在滑台上,可安装夹具,动力头等,通用性较好。 3 控制系统及特点 机床动作完全由气动控制,具备自锁,互锁功能及应付紧急情况的能力。系统原理图见图3。
1、4.手动推拉换向阀 2.按纽换向阀 3.气控换向阀 5.机控换向阀(直动式) 6.机控换向阀(通过式)7.单击阀(当入口进气时而出口只出一个脉冲气) 8.梭阀 9.调速阀 10.气源三联件 11.气源分配板 图3 系统原理图
1) 动作说明:在Ⅰ工位装上工件,按下夹紧阀1,夹紧气缸把工件夹紧→按下起动阀2,阀3A、3B换向,左铣动力头和右钻动力头同时起动,加工到位碰上行程开关5B、5C后快速退回→到原位后压下行程开关5A、5D→阀3C换向,夹具滑台移到Ⅱ工位,压下行程开关6→阀3D、3E、3F换向,左钻动力头,后铣动力头,右铣动力头同时起动,加工到位压下行程开关5F、5G、5I后快速退回,到原位后压下行程开关5E、5H、5J→阀3C换向,夹具滑台快速退回到Ⅰ工位→卸下工件,完成一个工作循环。
2) 系统特点:
a) 工件不夹紧,整个机床无法动作;
b) 夹具滑台不到位,动力头无法动作;
c) 动力头不在原位,夹具滑台无法动作;
d) 遇到异常情况(如断刀等),可按下紧急阀3按钮,所有梭阀换向,气控阀换向,正在加工的动力头立即退回原位;
e) 可单个或几个动力头加工:如果想某个动力头(如左铣动力头)工作,而其他动力头不工作,可以把4B、4C、4D、4E、阀门关上,这几个动力头就不工作;
f) 左右动力头加工完后,退回有快有慢,阀5A、5D串联后,只有在两个动力头退回到原位,阀ID才会通气换向,夹具滑台才会前进。避免了某个动力头因某种原因未及时退回而夹具滑台又已起动造成打刀等事故。阀5E、5H、5J串联亦如此。
g) 选用标准气动元件安装、调整方便,结构紧凑,成本低。 4 结论 该机床经过长期的使用证明,原5次定位改为1次定位加工完成,使加工精度大为提高。由于工序集中,机床性能可靠,操作方便,自动化程度高,原5个工人操作现只需1人,生产节拍为8s,仅为原来的1/5,使生产效率大为提高,完全可以满足大批量生产的要求,此机床可在类似场合推广使用
1 问题的提出及设计方案的确定 我公司燃气灶中气阀芯(见图1)从单轴纵切自动车床加工后,仍有2个孔、3条槽需要加工。以前加工的工艺方法是用仪表车床开槽,用台钻钻孔,分5道工序完成。这种加工方法存在以下缺点:①因多次定位,零件加工精度难以保障;②生产效率低,完成这5道工序需5台机床,5个工人,生产节拍为40 s;③自动化程度低。为了解决这些问题,我们设想把这5道工序合为1道工序,安排在同一机床上1次装夹完成加工。根据被加工件为铜材,材质较软,切削力小的特点,设计了1台采用全气控气动加工卧式三面双工位钻钻孔、铣槽平面组合机床。
2 机床的主要结构 1) 机床结构形式
该机床有钻孔动力头装置、铣削动力头装置、专用夹具、滑台、床身等。整个机床加工采用两工位布置,考虑到被加工件切削量小,本机床不设冷却系统(见图2)。
2) 特点
a) 钻孔动力头:采用日本SUGINO公司生产的气动进给动力头。其主要技术参数为最大钻孔直径8 mm,最大行程100 mm,主轴径向跳动精度≤0.01 mm,滑套轴线与固定套轴线移动方向平行度≤0.02 mm。其特点是加工精度高,动力头完全是气控、气动,配以可调节流器和液压阻尼器,可以实现对快进和工进速度的任意调节,且安装方便。
b) 铣削动力头装置:铣削头为自行设计,考虑它作为以后的通用件,设计此动力头在X、Y、Z3个方向均可以在一定范围调整。该铣削头装在滑台上,通过气缸驱动加上液压阻尼器,可进行快进和工进,在铣头原位和终点设置了气动行程开关。
c) 滑台:该滑台采用燕尾导轨,内有可调镶条,刚性好,工作稳定可靠,由气缸驱动。在滑台上,可安装夹具,动力头等,通用性较好。 3 控制系统及特点 机床动作完全由气动控制,具备自锁,互锁功能及应付紧急情况的能力。系统原理图见图3。
1、4.手动推拉换向阀 2.按纽换向阀 3.气控换向阀 5.机控换向阀(直动式) 6.机控换向阀(通过式)7.单击阀(当入口进气时而出口只出一个脉冲气) 8.梭阀 9.调速阀 10.气源三联件 11.气源分配板 图3 系统原理图
1) 动作说明:在Ⅰ工位装上工件,按下夹紧阀1,夹紧气缸把工件夹紧→按下起动阀2,阀3A、3B换向,左铣动力头和右钻动力头同时起动,加工到位碰上行程开关5B、5C后快速退回→到原位后压下行程开关5A、5D→阀3C换向,夹具滑台移到Ⅱ工位,压下行程开关6→阀3D、3E、3F换向,左钻动力头,后铣动力头,右铣动力头同时起动,加工到位压下行程开关5F、5G、5I后快速退回,到原位后压下行程开关5E、5H、5J→阀3C换向,夹具滑台快速退回到Ⅰ工位→卸下工件,完成一个工作循环。
2) 系统特点:
a) 工件不夹紧,整个机床无法动作;
b) 夹具滑台不到位,动力头无法动作;
c) 动力头不在原位,夹具滑台无法动作;
d) 遇到异常情况(如断刀等),可按下紧急阀3按钮,所有梭阀换向,气控阀换向,正在加工的动力头立即退回原位;
e) 可单个或几个动力头加工:如果想某个动力头(如左铣动力头)工作,而其他动力头不工作,可以把4B、4C、4D、4E、阀门关上,这几个动力头就不工作;
f) 左右动力头加工完后,退回有快有慢,阀5A、5D串联后,只有在两个动力头退回到原位,阀ID才会通气换向,夹具滑台才会前进。避免了某个动力头因某种原因未及时退回而夹具滑台又已起动造成打刀等事故。阀5E、5H、5J串联亦如此。
g) 选用标准气动元件安装、调整方便,结构紧凑,成本低。 4 结论 该机床经过长期的使用证明,原5次定位改为1次定位加工完成,使加工精度大为提高。由于工序集中,机床性能可靠,操作方便,自动化程度高,原5个工人操作现只需1人,生产节拍为8s,仅为原来的1/5,使生产效率大为提高,完全可以满足大批量生产的要求,此机床可在类似场合推广使用
电、气动自动进给钻削动力头的研制 摘要:本文介绍了电、气动自动进给钻削动力头的工作原理和基本结构,并详细进行了动力头运动分析和设计计算。 关键词:钻削动力头 工作原理 设计计算 1 概述 随着科学技术的迅速发展和规模化工业生产的需要,采用专用装备组合成现代化高速流水线和多功能高效组合机床,在许多行业中已成为保证产品的加工精度、降低生产成本、提高劳动生产率和企业竞争力的关键措施之一。动力头是组合机床的重要动力部件,其质量和性能的优劣直接影响到整台机床性能的好坏,但在一般的组合机床设计中,动力头只能提供主运动,其进给运动是由与之相配套的液压或机械滑台来实现的,这就给组合机床的设计和制造带来了较大的困难。为此,笔者在消化吸收国外先进技术的基础上,研制设计了一种新型的电、气动自动进给钻削动力头,如图1所示。气动控制与液压阻尼系统如图2所示。 |
1.液压调速器 2.同步带轮 3.轴承 4.密封圈 5.花键轴 6.密封圈 7.轴承 8.钻夹头 9.活塞杆 10.主轴 11.气缸体 12.轴承 13.托架 14.电机 15.同步带 16.后盖 图1 |
图2 2 电、气动自动进给动力头的主要结构特点 电、气动自动进给钻削动力头由主运动、进给运动和控制系统三部分组成。 (1)主运动 电、气动自动进给钻削动力头的主运动采用三相异步电机驱动,经同步齿形带及花键轴将电机的转矩传递给主轴,不同的主轴转速可由更换不同的同步齿形带轮来实现。由于动力头的主运动采用电机驱动,主轴的转速特性好,输出功率和转矩大,能适应于多轴钻削和较大孔径的加工工况。 (2)进给运动 由于气压传动具有动作反应快、环境的适应性好、结构简单、体积小等优点,并能实现无级调速,工作寿命长,动力源来源方便,因此,动力头的进给运动采用压缩空气作为动力源。考虑到空气的可压缩性,载荷变化时动力头的运动的平稳性较差,工进速度的调整和控制采用液压调速器来实现,动力头的快进和快退速度分别用排气节流阀来调整。 (3)控制系统 电、气动自动进给钻削动力头的进给运动采用了压缩空气为动力源,其进给运动的控制也采用了气动控制系统,由一个二位五通气控阀、一个机动阀、二个手动阀,若干个节流阀和两个外部控制气源口组成,结构紧凑,具有手动和远距离控制操作功能及原位、前位信号和复位信号保护功能。动力头快进行程和工进行程可通过挡铁连续可调。 (4)机械结构特点 电、气动自动进给钻削动力头是一个集动力头的主运动、进给运动和控制装置于一体的钻削动力头,为了实现其外形的紧凑,本动力头采用主轴嵌入气缸结构,主轴与活塞杆同心,活塞杆是空心的。里面装有进口的滚动轴承,以提高主轴的回转精度,主轴安装在轴承上,由同步带通过花键与电机连接,气缸体固定在托架上,活塞杆上装有液压调速器和行程调整螺钉,通过调整螺钉碰撞限位开关,实现动力头主轴的复位。 3 参数计算 电、气动自动进给钻削动力头设计参数主要是由规定的工件最大孔径钻削参数来确定。故电、气动自动进给钻削动力头的参数计算,必须由钻削工艺参数计算开始。 (1)钻削力的计算公式 (1) 式中: F——钻削过程中所需要的钻削力,N; CF——材料系数; dO——工件加工的孔径,mm; XF——等于1; YF——等于0.7; f——进给量,mm/r; KF——工件的硬度系数。 (2)钻削扭矩计算公式 (2) 式中: M——钻削过程中所需要的扭矩,N.m; CM——材料系数; dO——工件加工的孔径,mm; XM——等于1.9; YM——等于0.8; f——进给量,mm/r; KM——工件的硬度系数。 (3)钻削功率的计算公式 PM=2πMn.10-3 (3) 式中: PM——钻削过程中所需要的功率; n——钻头的转速,r/s。 (4)动力头推进力的计算公式 F=π(D2-d2)pη/4 (4) 式中: F——动力头的推动力,N; D——活塞直径,mm; d——活塞杆直径,mm; p——供气压力,MPa; η——效率系数(0.85) (5)耗气量的计算公式 Q=πS(2D2-d2)ηv.10-9/(4t) (5) 式中:Q——在工作压力下的耗气量,m3/s; S——最大行程,mm; t——往返时间,s; ηv——气容效率(0.9) (6)主要参数计算结果 已知设计参数为: 主轴转速:n=2050r/min 电机功率:P=0.55kW 最大推动力:F=1800N 最大行程:s=100mm 加工件最大孔径:do=4.5mm(钢) CF=833.85 XF=1.0 YF=0.7 KF=1.0 CM=333.54 XM=1.9 YM=0.8 KM=1.0 f=0.17 p=0.5 η=0.85 ηv=0.9 d=35mm D=80mm t=10 将以上数据分别代入式(1)、(2)、(3)、(4)、(5)中,得到: |
钻削力F=1085N 钻削扭矩M=1.4N.m 钻削功率PM=0.3kW |
推进力F=1692N 耗气量Q=0.001m3/s |
4 应用实例 电、气动自动进给钻削动力头作为组合机床的重要动力部件之一,在汽车工业、家电工业和摩托车制造业应用中所带来的巨大经济效益,已被国内外许多生产厂家的实践所证明。该动力头由广州机床研究所研制并生产出来之后,深得广大用户的青睐。已在轻工业、电梯制造业及其他机械加工行业得到了广泛的应用,并获得可观的经济效益。 5 结束语 (1)电、气动自动进给钻削动力头是一种集动力头的主运动、进给运动和控制系统于一体的高新技术产品,是机、电、气、液多项技术综合应用的结果。 (2)作为组合机床的重要动力部件之一,电、气动自动进给钻削动力头具有体积小、重量轻、结构紧凑、实用面广、组合多变等优点,能够根据用户的需要组合成多种形式的组合机床。 (3)电、气动自动进给钻削动力头的的旋转运动(主运动)采用电机通过同步带直接驱动,进给运动采用压缩空气作为动力源,实现主轴“快进—工进—快退”的自动循环,进给运动采用液压阻尼,进给速度无级可调,进给行程连续可调,钻削功率大,能同时驱动多根钻轴工作。 |
展开